Redrow's Sustainable Solutions come to Alconbury Weald
- 19.05.2017
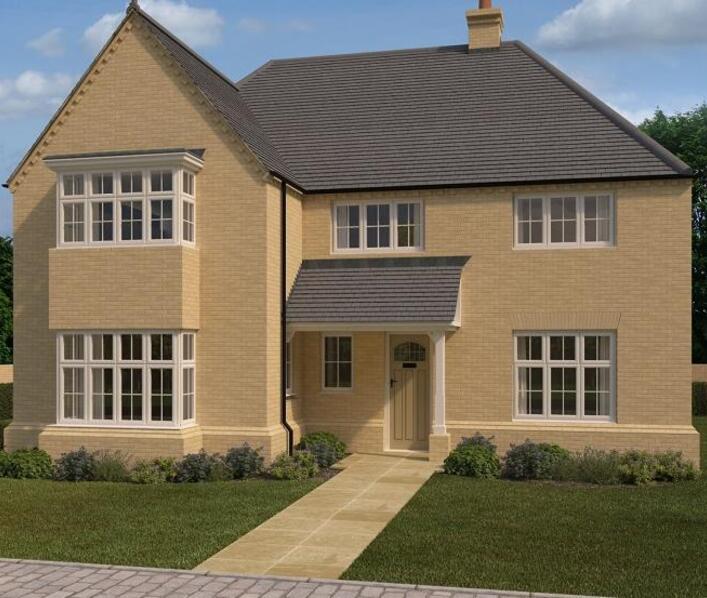
Timber frames are being used in the construction of the new Redrow homes at Alconbury Weald, offering a sustainable solution to a supply shortage while speeding up the build process.
The use of timber frames means that buyers should find that not only will their home be built quicker, enabling them to move sooner, they will also be able to decorate immediately.
Tonia Tyler, sales director for Redrow Homes, said:
“A lot of people who’ve enquired about the homes we’re building at Alconbury Weald have been surprised to learn that we’re using timber frames. One of the reasons we’ve reverted to this traditional method is to overcome a shortage of concrete blocks, but it’s also a fast, reliable and sustainable technique enabling each home to be made watertight quicker so the components aren’t exposed to the elements.”
The UK Timber Frame Association says early hardwood timber frame properties date back to Medieval and Tudor times; while softwood timber frame homes have been built in increasing numbers since the 18th century. In timber frame homes, concrete blockwork in the external walls are replaced by a structural insulated timber frame, which supports all the loads.
“At Alconbury Weald the timber frames will be cladded with bricks or render, so from the external skin it would be difficult for people to tell what method had been used to construct the property,” Tonia says.
While the use of timber frame comes at an extra cost to Redrow, the company believes that the ensuing benefits and time saved make it worthwhile both to them and to customers. Redrow was the first major UK housebuilder to score a maximum rating of ‘three trees’ from the WWF with 99.83% of timber sustainability sourced.
“We recognise that there’s a greater environmental awareness among homeowners and are proud of our record in sourcing timber sustainably. We only use timber from credible, certified legal and well managed sources, with minimal energy used to fell, mill and transport the wood before the frames are constructed,” Tonia adds.
“The advantage of the frames being precision-engineered under factory conditions is that room dimensions are more accurate, which is useful for fitting kitchens or carpets. Plus, because a ‘dry’ plasterboard lining system is used our homeowners can decorate straight away, without having to wait for the property to dry out first.”
Redrow’s current availability at Alconbury Weald includes four-bedroom homes in a choice of styles, priced from £339,950.
The new neighbourhood is already home to a new school, gym and café, with a community park, play facility and shop coming soon.
The Redrow sales centre at the development is open daily from 10am to 5.30pm.
For more information call 01480 802430 or see www.redrow.co.uk/alconbury.
Background information
Redrow was established in 1974. Today, it is one of the most successful and acclaimed property developers in the UK, building around 5,000 premium quality family homes a year in prime locations across England and Wales. Over Redrow’s history spanning more than 40 years, it has earned a unique reputation for quality and building beautiful homes, which people love to live in. To help achieve this it also focusses on two other key areas: valuing people and creating outstanding locations. Implementing its strategy whilst engaging with colleagues and stakeholders helps Redrow deliver significant value to investors and the wider community. Redrow is listed on the London Stock Exchange and is a constituent of the FTSE 250 index. For the year ended 30th June 2016, the Group reported record revenues of £1.38 billion. Redrow has been awarded the ‘Best Large Housebuilder’ title twice in the last three years at the What House? Awards. This year, Redrow was named as a UK Top 100 Apprenticeship Employer for the fourth consecutive year. Visit redrow.co.uk for more details.
Redrow at Alconbury WealdRedrow Homes